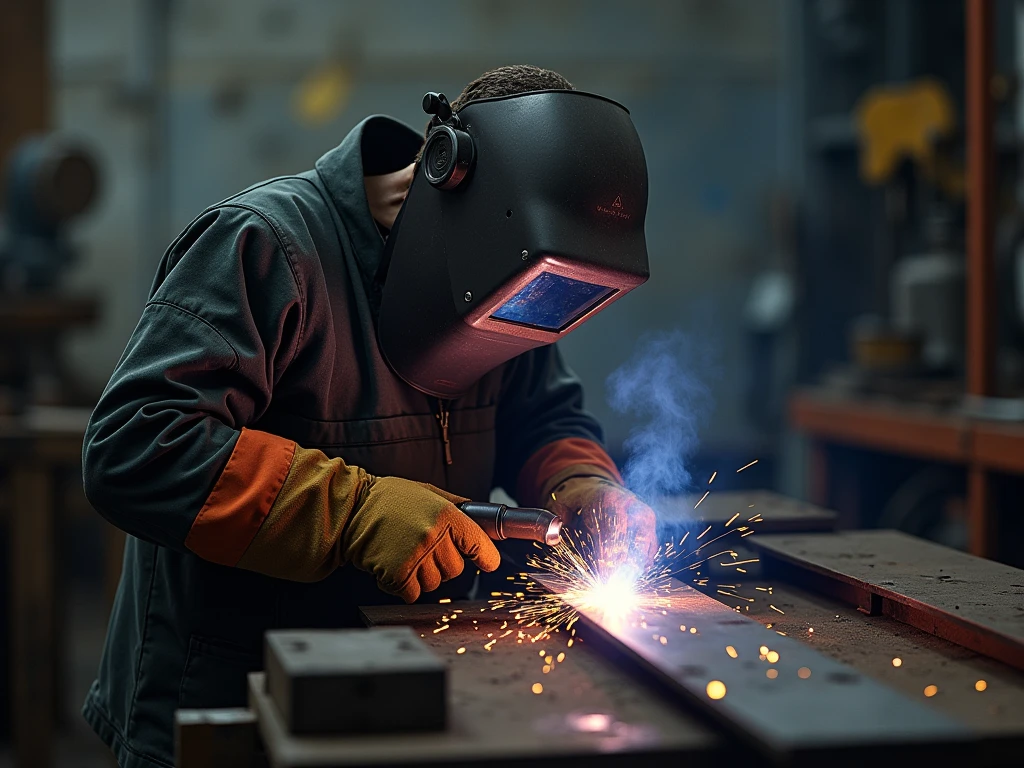
Metal Inert Gas (MIG) welding, also known as Gas Metal Arc Welding (GMAW), is one of the most widely used and versatile welding processes in the world. It is employed across industries such as automotive manufacturing, construction, shipbuilding, and general metal fabrication. MIG welding is favored for its speed, ease of use, and ability to weld a wide range of materials and thicknesses. The MIG welder, a professional who operates the MIG welding equipment, plays a vital role in ensuring that high-quality, durable, and precise welds are made, making them an integral part of many industries.
This article will explore the role of a MIG welder, the key responsibilities, skills required, the equipment used, the advantages of MIG welding, and how MIG welders contribute to modern industrial and manufacturing practices.
What is MIG Welding?
MIG welding is a type of welding process that uses a continuous wire electrode and an inert gas to create a weld. The process involves feeding the wire electrode from a spool through the welding gun, where it melts and fuses the workpieces together. An inert gas, usually argon or a mixture of argon and carbon dioxide, is used to shield the weld pool from contaminants in the air. MIG welding is highly efficient, providing strong, clean, and visually appealing welds.
MIG welding is particularly suitable for welding thin to medium-thick materials, including metals like steel, stainless steel, aluminum, and copper alloys. It’s widely used in industries that require a fast and cost-effective welding method without sacrificing quality.
Role of a MIG Welder
A MIG welder is a skilled professional responsible for operating MIG welding machines to create strong, precise welds. MIG welders are crucial in various fields, including automotive, aerospace, manufacturing, construction, and repair services. Their work ensures that components and structures are joined securely, maintaining the integrity and longevity of the final product.
The main tasks of a MIG welder typically include:
- Preparing the Workpieces: Before starting the welding process, MIG welders prepare the workpieces by cleaning the metal surfaces to remove dirt, rust, oil, or any other contaminants that could interfere with the weld quality. This step is vital, as it ensures a clean, strong bond between the materials.
- Setting Up the MIG Welder: MIG welders are responsible for setting up the welding machine and ensuring it is calibrated correctly. This includes adjusting the welding voltage, wire feed speed, and gas flow rate to suit the materials being welded and the specific welding conditions. They also choose the correct type of wire and gas mixture for the job.
- Performing the Welding Process: Once the machine is set up, the MIG welder uses the welding gun to melt the wire electrode, which then fuses the metal workpieces together. MIG welding is a relatively fast process, and the welder must control the gun and the speed of the weld to ensure consistency and high-quality welds.
- Monitoring the Weld: MIG welders must carefully monitor the welding process to avoid defects such as porosity, cracks, or incomplete fusion. They need to pay attention to the appearance of the weld bead to ensure it has the correct shape and penetration. If issues arise, MIG welders may need to stop the welding process and troubleshoot the problem.
- Post-Welding Inspection: After completing a weld, MIG welders conduct visual inspections to ensure the quality and integrity of the weld. They may also conduct additional tests, such as X-rays or ultrasonic inspections, to ensure the weld meets the required specifications.
- Maintaining the Equipment: MIG welders are also responsible for maintaining their welding equipment, including cleaning the welding gun, changing the wire spool, and checking the gas supply. Regular maintenance ensures that the equipment functions optimally and reduces the risk of malfunctions during critical operations.
Skills and Qualifications Required for a MIG Welder
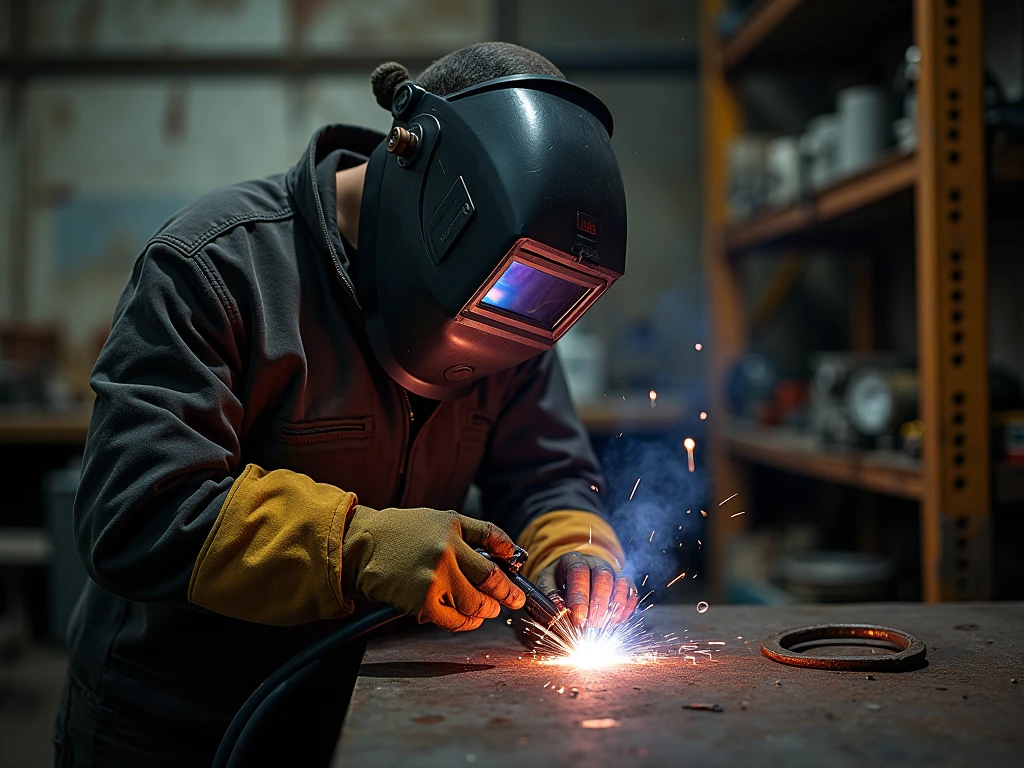
This article will explore the role of a MIG welder, the key responsibilities, skills required, the equipment used, the advantages of MIG welding, and how MIG welders contribute to modern industrial and manufacturing practices.
What is MIG Welding?
MIG welding is a type of welding process that uses a continuous wire electrode and an inert gas to create a weld. The process involves feeding the wire electrode from a spool through the welding gun, where it melts and fuses the workpieces together. An inert gas, usually argon or a mixture of argon and carbon dioxide, is used to shield the weld pool from contaminants in the air. MIG welding is highly efficient, providing strong, clean, and visually appealing welds.
MIG welding is particularly suitable for welding thin to medium-thick materials, including metals like steel, stainless steel, aluminum, and copper alloys. It’s widely used in industries that require a fast and cost-effective welding method without sacrificing quality.
Role of a MIG Welder
A MIG welder is a skilled professional responsible for operating MIG welding machines to create strong, precise welds. MIG welders are crucial in various fields, including automotive, aerospace, manufacturing, construction, and repair services. Their work ensures that components and structures are joined securely, maintaining the integrity and longevity of the final product.
The main tasks of a MIG welder typically include:
Preparing the Workpieces: Before starting the welding process, MIG welders prepare the workpieces by cleaning the metal surfaces to remove dirt, rust, oil, or any other contaminants that could interfere with the weld quality. This step is vital, as it ensures a clean, strong bond between the materials.
Setting Up the MIG Welder: MIG welders are responsible for setting up the welding machine and ensuring it is calibrated correctly. This includes adjusting the welding voltage, wire feed speed, and gas flow rate to suit the materials being welded and the specific welding conditions. They also choose the correct type of wire and gas mixture for the job.
Performing the Welding Process: Once the machine is set up, the MIG welder uses the welding gun to melt the wire electrode, which then fuses the metal workpieces together. MIG welding is a relatively fast process, and the welder must control the gun and the speed of the weld to ensure consistency and high-quality welds.
Monitoring the Weld: MIG welders must carefully monitor the welding process to avoid defects such as porosity, cracks, or incomplete fusion. They need to pay attention to the appearance of the weld bead to ensure it has the correct shape and penetration. If issues arise, MIG welders may need to stop the welding process and troubleshoot the problem.
Post-Welding Inspection: After completing a weld, MIG welders conduct visual inspections to ensure the quality and integrity of the weld. They may also conduct additional tests, such as X-rays or ultrasonic inspections, to ensure the weld meets the required specifications.
Maintaining the Equipment: MIG welders are also responsible for maintaining their welding equipment, including cleaning the welding gun, changing the wire spool, and checking the gas supply. Regular maintenance ensures that the equipment functions optimally and reduces the risk of malfunctions during critical operations.
Skills and Qualifications Required for a MIG Welder
MIG welding is a precise skill that requires knowledge of welding techniques, materials, and safety protocols. Below are some of the key skills and qualifications required for a MIG welder:
Welding Skills: A MIG welder must have a solid understanding of the MIG welding process, including how to set up the machine, adjust settings, and create clean, strong welds. Proficiency in welding different types of metals, such as steel, stainless steel, and aluminum, is essential, as each material requires specific techniques and settings.
Blueprint Reading: MIG welders often need to read and interpret blueprints, technical drawings, and welding symbols to ensure they are following the correct specifications for the project. Being able to understand the dimensions and welding positions indicated in these drawings is critical for successful execution.
Attention to Detail: The ability to spot flaws and imperfections in a weld is a critical skill for MIG welders. They must ensure that each weld is strong, visually appealing, and free from defects. Small issues can lead to structural failure, so meticulous attention to detail is essential.
Mechanical Aptitude: MIG welders should have a good understanding of how the welding equipment works and how to troubleshoot common problems. This mechanical knowledge helps them identify and address issues such as incorrect wire feed or gas flow, ensuring the equipment operates effectively.
Safety Awareness: MIG welders must adhere to strict safety protocols to prevent accidents and injuries. This includes wearing protective gear such as welding helmets, gloves, protective clothing, and face shields. They must also ensure that their work environment is safe and free from flammable materials, as welding involves high heat and can create sparks.
Physical Stamina: MIG welding can be physically demanding. Welders may have to work in awkward positions for extended periods or in confined spaces, especially when working on larger structures or components. Good hand-eye coordination and physical endurance are vital for maintaining consistent, high-quality welds.
Problem-Solving Skills: MIG welders need to be able to troubleshoot issues that arise during the welding process. Whether it’s a problem with the equipment or the appearance of the weld, being able to diagnose and fix the problem is essential for maintaining the quality of the work.
Certification: Although it’s not always mandatory, many MIG welders pursue certification from professional organizations such as the American Welding Society (AWS) or similar institutions. Certification demonstrates that the welder has the necessary skills and knowledge to perform MIG welding according to industry standards.
MIG Welding Equipment
MIG welding requires specific equipment to operate effectively. The primary components include:
MIG Welding Machine: This is the core of the MIG welding process. It provides the power needed to create the heat necessary for welding. The machine controls the voltage and current, which determine the quality of the weld. Modern MIG machines often feature advanced settings that allow the welder to adjust the machine’s parameters for different materials and applications.
Welding Gun: The welding gun holds the wire electrode and directs the shielding gas to the weld pool. It also controls the feed of the wire, which is crucial for a consistent and strong weld. MIG welders must handle the gun with precision to ensure the quality of the weld.
Wire Electrode: The wire electrode is a continuously fed wire that melts during the welding process, fusing the materials together. The type of wire used depends on the material being welded and the welding conditions. Common wire materials include solid wire, flux-cored wire, and alloy wires.
Shielding Gas: In MIG welding, an inert gas (usually argon or a mixture of argon and carbon dioxide) is used to shield the weld pool from contaminants in the air. This gas helps create a clean weld and prevents oxidation or other atmospheric issues that could compromise the weld’s integrity.
Protective Gear: Due to the high heat and sparks generated during the welding process, protective gear is essential for a MIG welder. This includes welding helmets with auto-darkening filters, flame-resistant gloves, jackets, and protective eyewear.
Advantages of MIG Welding
MIG welding offers numerous benefits, which is why it is one of the most commonly used welding processes in various industries. Some of the key advantages include:
Speed: MIG welding is faster than many other welding techniques, such as Stick welding, making it ideal for large-scale production runs and high-volume manufacturing.
Ease of Use: MIG welding is relatively easy to learn compared to other welding techniques. The process is more forgiving, which makes it suitable for both beginners and experienced welders.
Clean Welds: MIG welding produces smooth, clean, and aesthetically appealing welds. The use of shielding gas helps reduce spatter and prevents oxidation, resulting in high-quality welds with minimal cleanup required.
Versatility: MIG welding can be used on a wide range of materials, including various types of steel, stainless steel, aluminum, and alloys. It can also be used on a broad range of thicknesses, from thin sheet metal to thicker plates.
Minimal Post-Weld Cleanup: Unlike Stick welding, MIG welding generates very little slag or spatter, reducing the need for extensive post-weld cleanup. This leads to better productivity and less material wastage.
Conclusion
MIG welding is a versatile, efficient, and widely used welding technique, and MIG welders are vital to ensuring the quality and durability of the final product. With the ability to weld a wide range of materials and perform both precision work and high-speed production, MIG welding is an essential process in industries like automotive, manufacturing, construction, and aerospace.
MIG welders are responsible for preparing workpieces, setting up the equipment, performing high-quality welds, and maintaining the machinery. Their skills and expertise contribute to the creation of strong, reliable, and safe products, ensuring that everything from cars to bridges are built to last. As industries continue to evolve and new materials and technologies emerge, MIG welders will remain essential to the manufacturing and construction sectors, playing a key role in the continued development of innovative, high-quality products.
MIG welding is a precise skill that requires knowledge of welding techniques, materials, and safety protocols. Below are some of the key skills and qualifications required for a MIG welder:
- Welding Skills: A MIG welder must have a solid understanding of the MIG welding process, including how to set up the machine, adjust settings, and create clean, strong welds. Proficiency in welding different types of metals, such as steel, stainless steel, and aluminum, is essential, as each material requires specific techniques and settings.
- Blueprint Reading: MIG welders often need to read and interpret blueprints, technical drawings, and welding symbols to ensure they are following the correct specifications for the project. Being able to understand the dimensions and welding positions indicated in these drawings is critical for successful execution.
- Attention to Detail: The ability to spot flaws and imperfections in a weld is a critical skill for MIG welders. They must ensure that each weld is strong, visually appealing, and free from defects. Small issues can lead to structural failure, so meticulous attention to detail is essential.
- Mechanical Aptitude: MIG welders should have a good understanding of how the welding equipment works and how to troubleshoot common problems. This mechanical knowledge helps them identify and address issues such as incorrect wire feed or gas flow, ensuring the equipment operates effectively.
- Safety Awareness: MIG welders must adhere to strict safety protocols to prevent accidents and injuries. This includes wearing protective gear such as welding helmets, gloves, protective clothing, and face shields. They must also ensure that their work environment is safe and free from flammable materials, as welding involves high heat and can create sparks.
- Physical Stamina: MIG welding can be physically demanding. Welders may have to work in awkward positions for extended periods or in confined spaces, especially when working on larger structures or components. Good hand-eye coordination and physical endurance are vital for maintaining consistent, high-quality welds.
- Problem-Solving Skills: MIG welders need to be able to troubleshoot issues that arise during the welding process. Whether it’s a problem with the equipment or the appearance of the weld, being able to diagnose and fix the problem is essential for maintaining the quality of the work.
- Certification: Although it’s not always mandatory, many MIG welders pursue certification from professional organizations such as the American Welding Society (AWS) or similar institutions. Certification demonstrates that the welder has the necessary skills and knowledge to perform MIG welding according to industry standards.
MIG Welding Equipment
MIG welding requires specific equipment to operate effectively. The primary components include:
- MIG Welding Machine: This is the core of the MIG welding process. It provides the power needed to create the heat necessary for welding. The machine controls the voltage and current, which determine the quality of the weld. Modern MIG machines often feature advanced settings that allow the welder to adjust the machine’s parameters for different materials and applications.
- Welding Gun: The welding gun holds the wire electrode and directs the shielding gas to the weld pool. It also controls the feed of the wire, which is crucial for a consistent and strong weld. MIG welders must handle the gun with precision to ensure the quality of the weld.
- Wire Electrode: The wire electrode is a continuously fed wire that melts during the welding process, fusing the materials together. The type of wire used depends on the material being welded and the welding conditions. Common wire materials include solid wire, flux-cored wire, and alloy wires.
- Shielding Gas: In MIG welding, an inert gas (usually argon or a mixture of argon and carbon dioxide) is used to shield the weld pool from contaminants in the air. This gas helps create a clean weld and prevents oxidation or other atmospheric issues that could compromise the weld’s integrity.
- Protective Gear: Due to the high heat and sparks generated during the welding process, protective gear is essential for a MIG welder. This includes welding helmets with auto-darkening filters, flame-resistant gloves, jackets, and protective eyewear.
Advantages of MIG Welding
MIG welding offers numerous benefits, which is why it is one of the most commonly used welding processes in various industries. Some of the key advantages include:
- Speed: MIG welding is faster than many other welding techniques, such as Stick welding, making it ideal for large-scale production runs and high-volume manufacturing.
- Ease of Use: MIG welding is relatively easy to learn compared to other welding techniques. The process is more forgiving, which makes it suitable for both beginners and experienced welders.
- Clean Welds: MIG welding produces smooth, clean, and aesthetically appealing welds. The use of shielding gas helps reduce spatter and prevents oxidation, resulting in high-quality welds with minimal cleanup required.
- Versatility: MIG welding can be used on a wide range of materials, including various types of steel, stainless steel, aluminum, and alloys. It can also be used on a broad range of thicknesses, from thin sheet metal to thicker plates.
- Minimal Post-Weld Cleanup: Unlike Stick welding, MIG welding generates very little slag or spatter, reducing the need for extensive post-weld cleanup. This leads to better productivity and less material wastage.
Conclusion
MIG welding is a versatile, efficient, and widely used welding technique, and MIG welders are vital to ensuring the quality and durability of the final product. With the ability to weld a wide range of materials and perform both precision work and high-speed production, MIG welding is an essential process in industries like automotive, manufacturing, construction, and aerospace.
MIG welders are responsible for preparing workpieces, setting up the equipment, performing high-quality welds, and maintaining the machinery. Their skills and expertise contribute to the creation of strong, reliable, and safe products, ensuring that everything from cars to bridges are built to last. As industries continue to evolve and new materials and technologies emerge, MIG welders will remain essential to the manufacturing and construction sectors, playing a key role in the continued development of innovative, high-quality products.