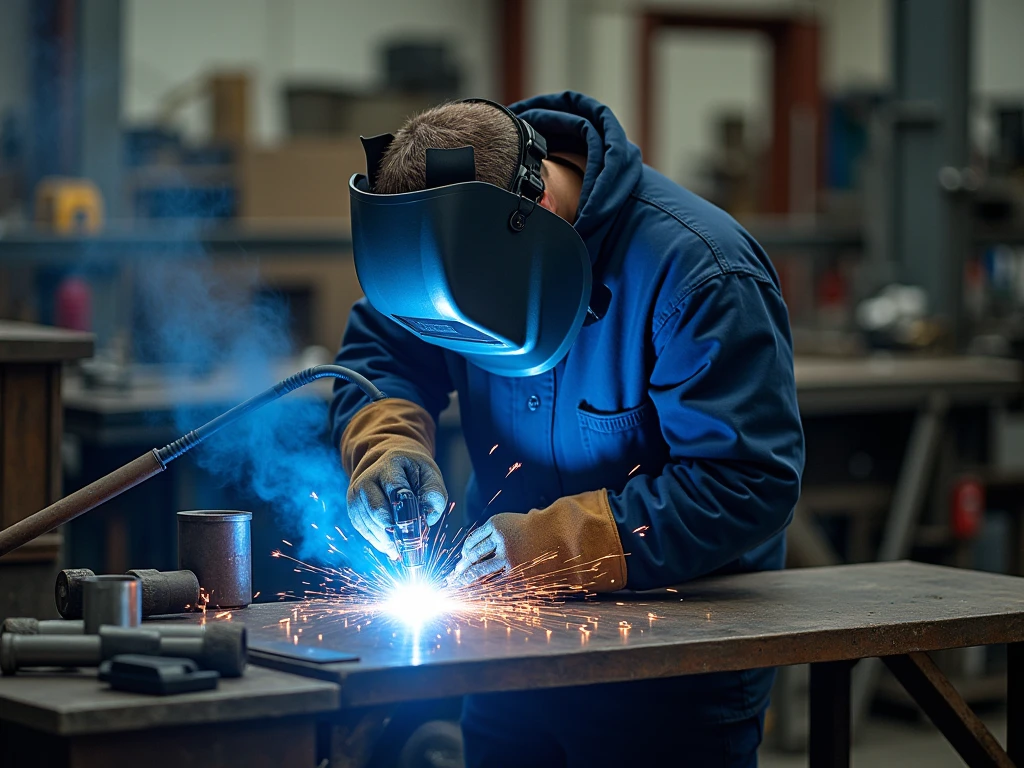
Welding technicians play a crucial role in the manufacturing, construction, and maintenance industries, ensuring that welded joints are both strong and durable. As experts in welding processes, materials, and safety standards, they are responsible for producing high-quality welds, maintaining equipment, and troubleshooting welding-related issues. Their skills are critical in producing everything from intricate parts in automotive factories to large-scale structures like bridges and skyscrapers. This article will explore the responsibilities, skills, qualifications, and work environments of welding technicians, as well as their importance across various industries.
What is a Welding Technician?
A welding technician is a skilled professional responsible for performing welding tasks, inspecting welds, and maintaining welding equipment. Unlike welding engineers who focus on designing and developing welding processes, welding technicians are hands-on practitioners who apply their technical expertise to ensure the success of welding projects. Their work is integral to ensuring the strength, durability, and safety of welded components, as they often work with metals like steel, aluminum, and stainless steel, which require specialized techniques.
Welding technicians can work in a variety of industries, from manufacturing to aerospace, automotive, shipbuilding, and construction. They are trained in various welding techniques, including TIG (Tungsten Inert Gas), MIG (Metal Inert Gas), Stick (Shielded Metal Arc Welding), and Flux-Cored Arc Welding (FCAW), each of which has its own application depending on the materials, joint configurations, and project specifications.
Primary Responsibilities of a Welding Technician
Welding technicians perform a range of tasks related to welding operations, from preparation to inspection. Their primary responsibilities include:
- Executing Welding Procedures: Welding technicians are responsible for performing various welding techniques to join metals, such as TIG, MIG, or Stick welding. They must determine which method is most appropriate for the material and the project requirements. They prepare and set up welding equipment, select the right filler materials, and execute the weld according to project specifications and safety standards.
- Equipment Setup and Maintenance: Welding technicians are responsible for setting up and maintaining welding equipment, such as welding machines, tools, and protective devices. They ensure that all equipment is functioning correctly and troubleshoot any issues with the machinery. Regular maintenance is essential for maintaining equipment efficiency and prolonging its lifespan.
- Quality Control and Inspection: One of the key responsibilities of a welding technician is to inspect welds and ensure they meet quality standards. This involves visually inspecting the finished welds and conducting non-destructive testing (NDT) methods such as ultrasonic, x-ray, or magnetic particle testing to detect flaws like cracks, voids, or porosity. Welding technicians may also be involved in performing destructive tests to confirm the weld’s strength and durability.
- Blueprint Interpretation and Planning: Welding technicians are often required to read and interpret blueprints, technical drawings, and welding symbols. Understanding these documents is crucial to ensure that the welding work aligns with the project’s design specifications. Accurate interpretation helps welding technicians produce welds that meet dimensional tolerances and functional requirements.
- Safety Compliance: Welding technicians must adhere to strict safety protocols to prevent accidents and ensure the well-being of themselves and their coworkers. They follow all safety regulations and use personal protective equipment (PPE) such as helmets, gloves, protective clothing, and respirators to minimize the risks associated with welding. Additionally, welding technicians ensure that the workspace is properly ventilated and that fire safety measures are in place.
- Troubleshooting and Problem-Solving: In the course of their work, welding technicians may encounter issues such as equipment malfunction, improper welds, or material defects. They must be able to identify the source of the problem and develop solutions to rectify the issue. This may involve adjusting welding parameters, repairing equipment, or reworking welds to meet quality standards.
- Collaboration and Communication: Welding technicians often work closely with engineers, fabricators, and other skilled tradespeople. They communicate with team members to ensure that welding processes are correctly applied, quality standards are met, and the work progresses according to the project timeline.
Skills and Qualifications of a Welding Technician
To become a successful welding technician, individuals must possess a combination of technical skills, hands-on experience, and problem-solving abilities. Below are the key skills and qualifications required for the role:
- Technical Welding Skills: A welding technician must be proficient in various welding techniques such as MIG, TIG, Stick, and FCAW. Each technique has its own advantages and applications, and technicians must be able to choose the most suitable method based on material, joint configuration, and project requirements.
- Blueprint Reading and Interpretation: Welding technicians need to be able to read and understand complex blueprints, technical drawings, and welding symbols. This skill is vital for determining the exact specifications for weld placement, material selection, and the dimensions of welded components.
- Attention to Detail: A key trait of any successful welding technician is the ability to pay close attention to detail. Small mistakes in welds can lead to significant structural issues, so welding technicians must be meticulous in every step of the process, from preparing materials to executing welds and performing inspections.
- Problem-Solving and Troubleshooting: Welding technicians are often faced with challenges on the job, whether it’s an equipment malfunction, a quality issue with a weld, or a technical problem. They must have strong problem-solving skills to diagnose issues and find effective solutions to keep the project on track.
- Knowledge of Materials: Welding technicians must have a deep understanding of different types of metals and materials, including their properties and how they respond to heat. This knowledge helps technicians select the appropriate welding method, filler material, and techniques for different materials, such as carbon steel, stainless steel, and aluminum.
- Safety Awareness: Welding is a hazardous occupation, involving risks such as exposure to high heat, fumes, and potential fire hazards. A welding technician must be well-versed in workplace safety protocols, proper use of PPE, and fire safety measures to mitigate these risks and ensure a safe working environment.
- Physical Stamina: Welding can be physically demanding, requiring technicians to work in challenging positions, such as lying on their back or working at great heights. The ability to work for long periods while maintaining precision is essential. Additionally, welding technicians must have good hand-eye coordination and steady hands to produce clean, strong welds.
- Education and Training: While some welding technicians may learn their trade through apprenticeships or on-the-job training, many pursue formal education. Technical schools and community colleges offer welding programs that provide in-depth knowledge of welding techniques, equipment, and safety protocols. Certifications from organizations such as the American Welding Society (AWS) are also beneficial for demonstrating competence and advancing in the field.
Work Environments for Welding Technicians
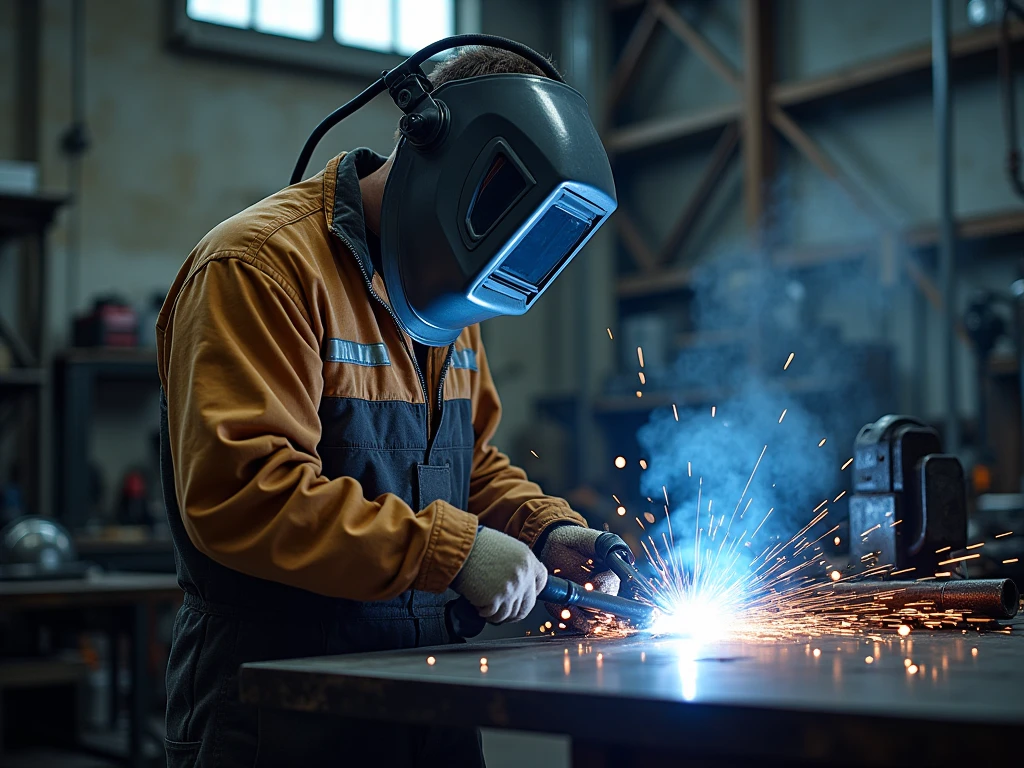
Welding technicians can work in a variety of settings, including:
- Manufacturing Plants: In manufacturing, welding technicians are involved in producing everything from automotive parts to heavy machinery. They work in factories where large-scale production requires efficient and high-quality welding to ensure that parts meet strict specifications.
- Construction Sites: In the construction industry, welding technicians are essential for assembling steel structures, bridges, and pipelines. They work outdoors and may be required to weld large components in place, often at great heights or in confined spaces.
- Shipbuilding: Welding technicians are employed in shipyards where they are responsible for welding metal hulls, decks, and other components of ships and submarines. This work requires precision and the ability to perform welds that can withstand the harsh marine environment.
- Oil and Gas: The oil and gas industry relies heavily on welding technicians to maintain and repair pipelines, drilling rigs, and offshore platforms. These workers must be able to perform welding in challenging environments, such as remote locations or underwater, where safety and accuracy are paramount.
- Aerospace: In the aerospace industry, welding technicians work with high-strength metals and specialized alloys to build or maintain aircraft components. The precision required in this field is exceptional, as even the smallest flaw in a weld could lead to catastrophic failure.
Conclusion
Welding technicians are essential professionals in industries where metalwork and structural integrity are of paramount importance. They combine technical welding skills, safety knowledge, and problem-solving abilities to execute high-quality welds and ensure the reliability of welded components. As industries continue to advance with new materials and technologies, the role of welding technicians will only become more vital, offering a rewarding career path for those who are passionate about welding and craftsmanship. With the right training, experience, and safety mindset, welding technicians have the opportunity to work in diverse and exciting industries, contributing to the development of everything from everyday products to critical infrastructure.